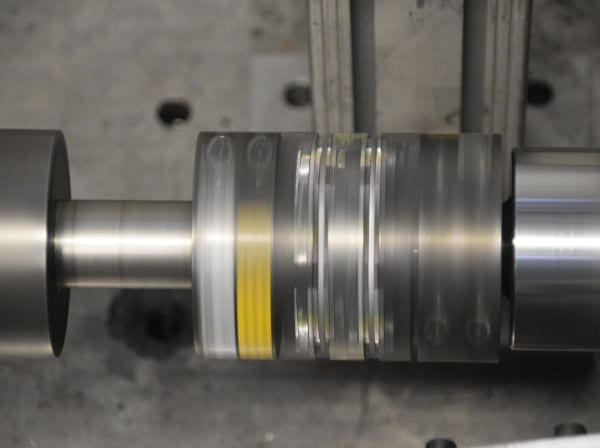
What we measure
Load types
Below we have summarized the different loads and forces we can subject a sample to in our test lab.
Tension/Compression

± 0 – 2,000 kN
up to 1,100 Hz
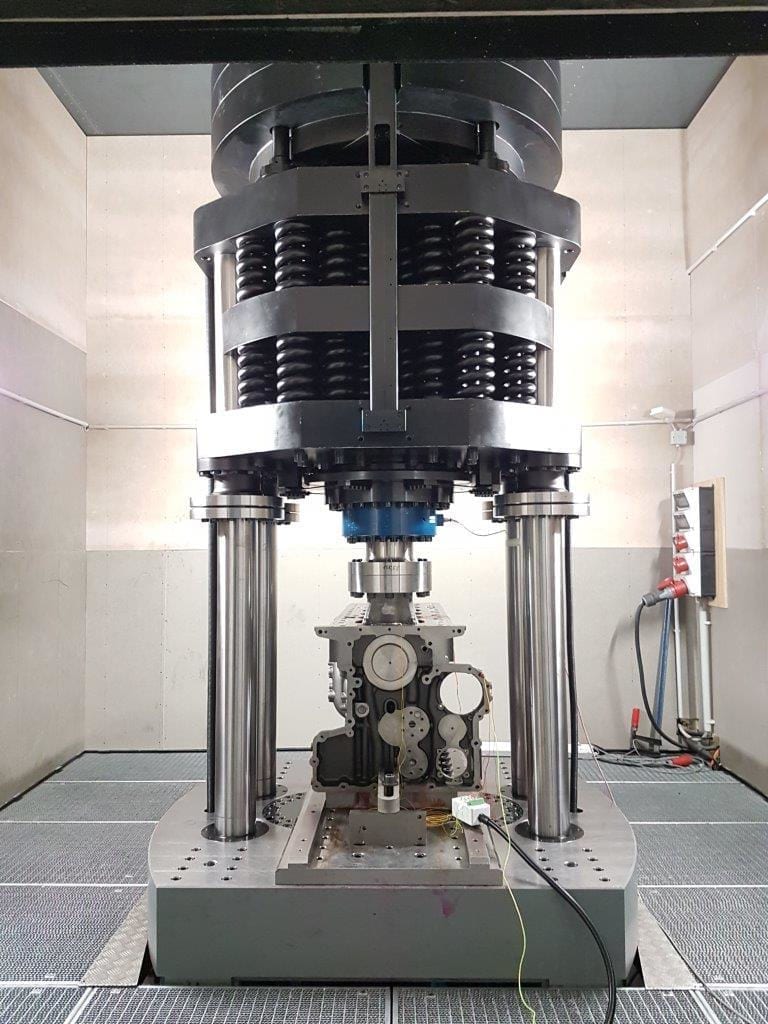
- Fatigue strength test
- Static tensile testing
- Investigate elastic and plastic deformation
- Operational load tracking test
- Up to 6 axes possible in multiaxial testing
- Verification of the areas of highest stress
We have many different test systems capable of axial load testing. You can select the amplitude and the middle load. Dynamic and quasi-static loads can be applied.
Commonly Tested Components:
- Connecting rods
- Screws, bolts
- Springs
- Material samples
- Twist-beam rear axles
- Plain and roller bearings
- Prosthesis
- Stents
Bending

± 0 – 500,000 Nm
up to 500 Hz
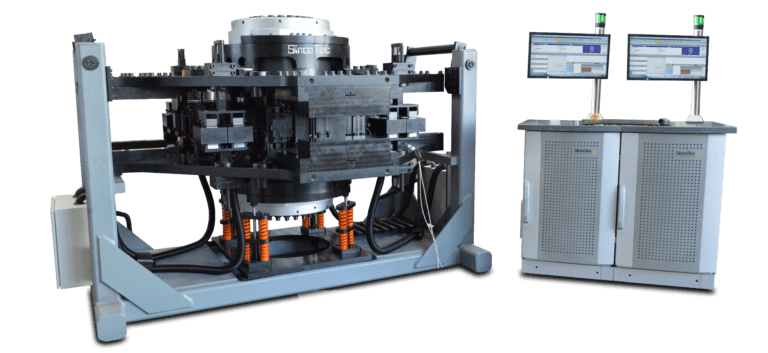
- Fatigue strength test
- Verification of the areas experiencing the highest load
- 3 and 4 point bending
- Static breaking load
- Investigate elastic and plastic deformation
We conduct three and four-point bending tests on components with our part-specific clamping devices which allow us to reduce lateral forces during bending to a minimum. We can also overlay bending and torsion forces of particular utility, for example, in the case of a crankshaft.
Commonly Tested Components:
- Crankshaft/crankshaft components
- Flywheels/Flywheel assembly
- Material samples
- Twist-beam rear axles
- Brackets
- Joints
- Gears
Torsion

±0 – 400,000 Nm
Between 0.1 – 500 Hz
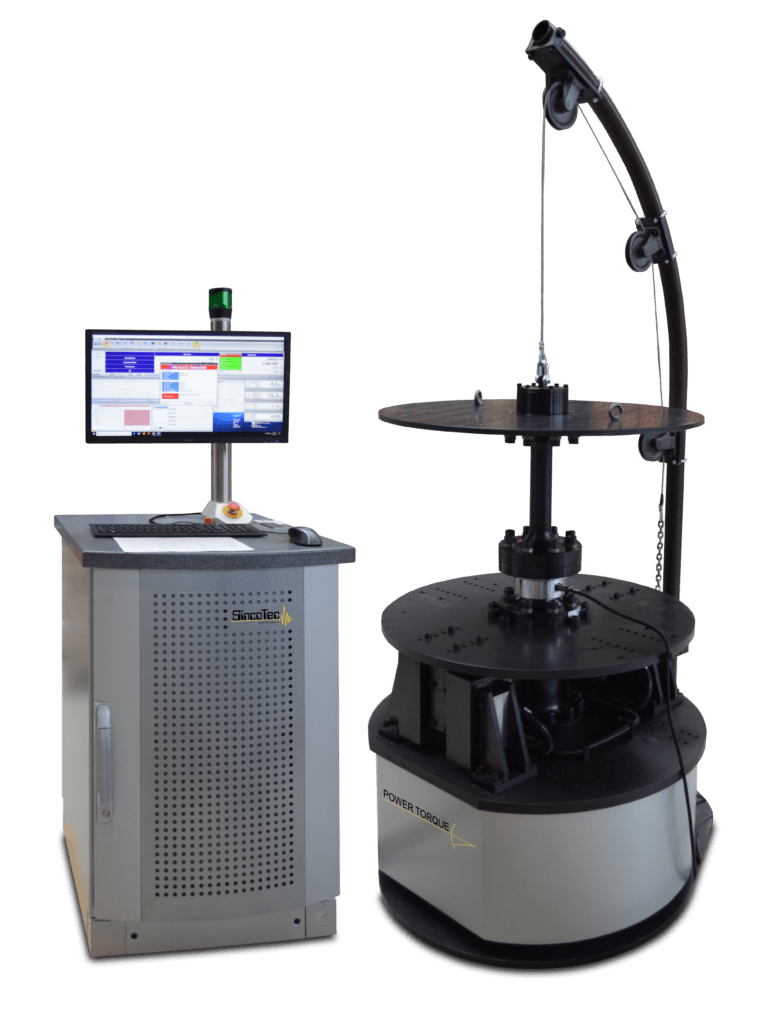
- Fatigue strength test
- Torsion angle
- Verification of the areas experiencing the highest stress
- Investigate elastic and plastic deformation
- Static breaking load
We generate the torsional moment through either direct drive or through a torsional spring-mass swing system. Tests can run with or without a mean load. It is also possible to determine the maximum torsion angle. Additionally, our resonance test systems offer highly accurate crack detection.
Commonly tested components:
- Crankshaft/crankshaft components
- Gear shaft
- Drive shaft
- Oil field drilling devices
- Twist-beam rear axles
- Clutch units
- Torsional vibration dampers
Internal Pressure

0.1 bar – 4,000 bar
up to 50 Hz
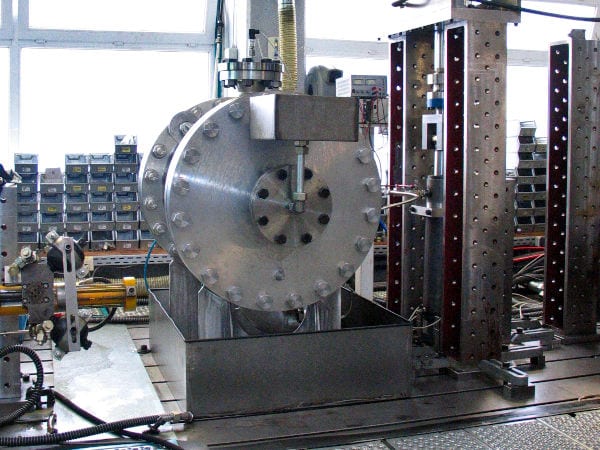
- Multi-sample testing
- Static and dynamic testing
In our high-pressure lab, we use both pneumatic actuators (up to 20 bar) and resonance-based test rigs (up to 4,000 bar). To deliver the most efficient test for you, our rigs test multiple samples simultaneously at test frequencies between 30 Hz-50 Hz. Even at such high pressures our drive systems are 5x faster and use 40x less energy than comparable forced-drive systems.
Do you need to validate parts or components subject to internal pressure? We offer fatigue testing using dynamic pressure-pulsators and
are additionally able to determine maximum burst pressures. The application actuator type (resonance, servo-hydraulic, pneumatic) is individually determined based on your requirement.
The test rig can also be configured with flammable FAM-testing medium, following DIN51604-B guidelines, as an alternative fuel source.
Commonly tested Components:
- Rails and fuel column
- Fuel filter
- Nozzles/jets
- Injectors
- Pipes
- Hoses
- Heat exchanger
- Any part or assembly subject to internal pressure
Rotational Bending

0 – 350,000 Nm
up to 300 Hz
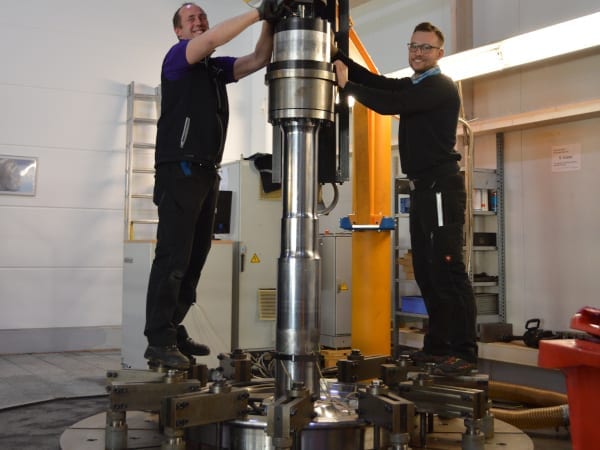
Many rotating parts experience additional bending moments. We are able to recreate these exact conditions using a variety of test systems. The sample can be anything from a small material sample to a railway wheelset. Additionally, we can offer crack propagation investigations. These allow us to assess changes in pre-existing damage up to a specific length for the duration of testing
Commonly tested components:
- Material samples
- Wheel bearings or passenger cars and trucks
- Railway wheelsets
- Pipes
- Drill pipes
- Camshafts
- Rotor shafts
- Motorcycle rims
Burst/Pulsating Spin

30,000 rpm
45,000 rpm
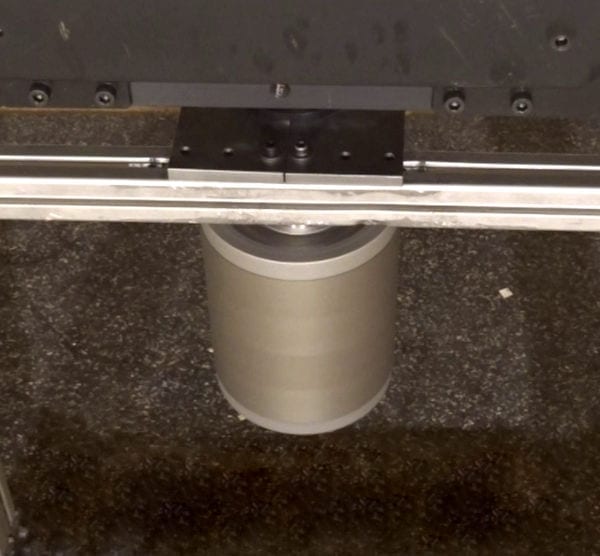
Tests can be carried out in either a vertical or a horizontal alignment of the sample. Our proprietary control systems allow us to set acceleration patterns customizing the test procedure to your requirements. During the test, elastic and plastic deformation of the rotor can be identified with dedicated displacement sensors even at temperatures up to 200 °C. Temperature can be increased and decreased throughout the testing process. Special containment vessels allow us to rotate samples until they fail during burst testing, determining their point of failure. In burst spin tests, highly accurate acceleration sensors are used for data collection.
Commonly Tested Components:
- Rotors of electric motors
- Flywheels
- Turbine wheels
- Milling and grinding tools
- Any rotational symmetric part or component
Vibration

Max. 22 kN and 70 kN
0.1 Hz to 4,000 Hz
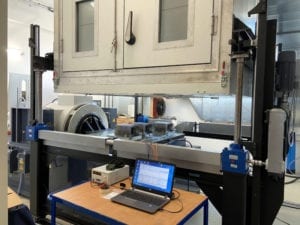
- Single axle vertical vibration testing under different types of loads
- Single axle, horizontal vibration testing with the help of sliding tables
- Signal types: sine, sweep, noise, shock, and resonance dwell tests
- Testing along three axes using servohydraulic vibration tables
- Combination with environmental simulations (cold, heat, temperature changes, and/or humidity)
- Combination with second load type (e.g. internal pressure or axial load)
- Additional signal forms: service load approach signal
Our Shaker can also handle larger components. Vibrations and jolts are used to recreate the mechanical loads that a component experiences. The loads applied are determined by norms, factory standards, or are derived from measurement data.
Environmental simulations can also be added to complement testing to, for example, simulate transportation simulations. Our experts are also able to determine frequency overshoots in your components.
Commonly tested Components:
- Track rod
- Stators
- Car body parts
- Containers/pumps
- Wires
Environmental Simulations

Temperature
(Norm)Dirt / Corrosion/ Hudmidity
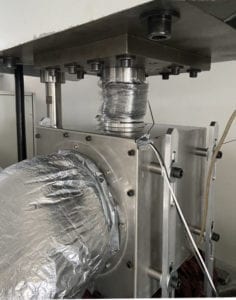
Commonly tested components:
- Material samples
- Passenger cars and truck wheel bearings
- Railroad wheelsets
- Pipes
- Drill pipes
- Camshafts
- Rotor shafts
- Motorcycle rims
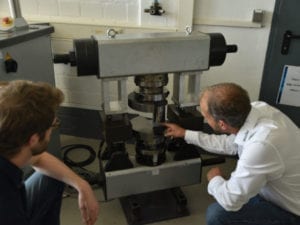
What do you want us to test?
We have testing solutions for all manner of components, assemblies, and materials to determine their fatigue strength, maximum load capacity, lifetime, and reliability. Contact us below with a summary of your testing needs and we will reach out to you as soon as possible.