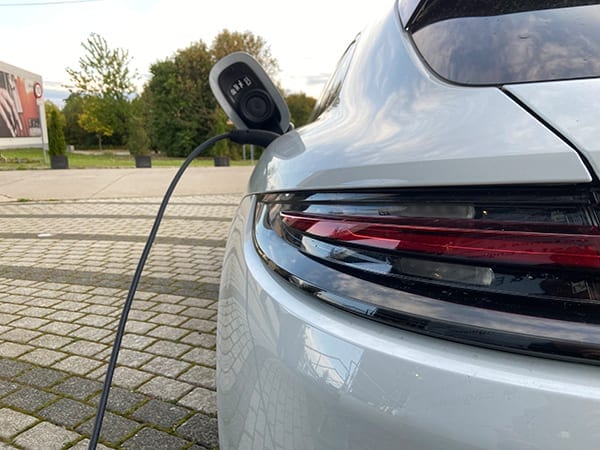
A typical application
Rotors
The future is electric and travel is ever more driven by the rotors of electric motors. Examining the dynamic strength of those rotors reduces outage times and the weight of the moving mass thereby increasing the range and agility of electric vehicles.
Currently, tests can be implemented up to 45,000 rpm and can be conducted at variable temperatures up to 200 °C.

Rotation speed change tests
- How much fatigue occurs under acceleration and braking on the rotor?
- Fatigue testing through cyclical acceleration and deceleration with defined acceleration ramps and stopping times.
- Special measurement technology allows us to measure the specimen in the lower µm-area during testing.
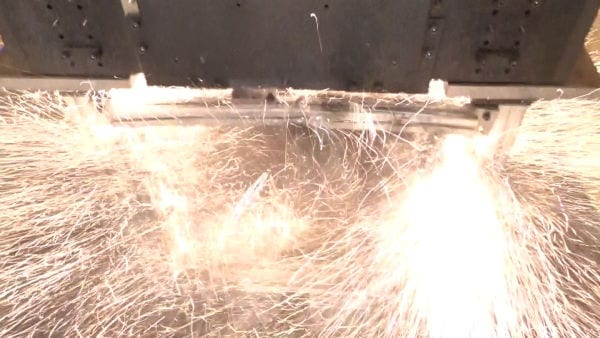
Spin and burst tests
- Apply centrifugal forces up to the material’s limit – what rotation speed is possible?
- Testing of component geometry and testing up to material limit can be completed using our test rigs.
- Special infrastructure allows us to test up to and past material limits.
Do your components need to be tested?
We have testing solutions for all manner of components, assemblies, and materials to determine their fatigue strength, maximum load capacity, lifetime, and reliability. Contact us below with a summary of your testing needs and we will reach out to you as soon as possible.