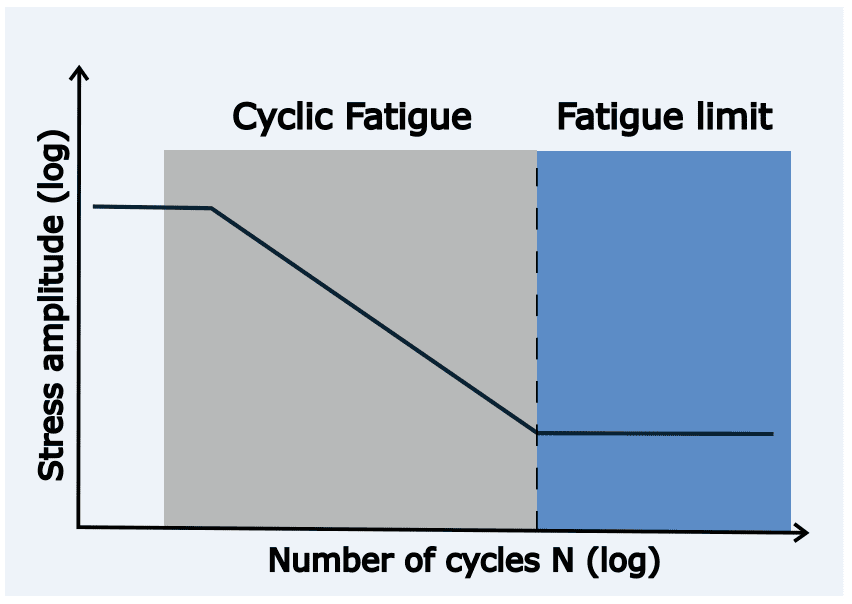
Fatigue Strength
Fatigue strength deals with the fatigue and operational design of components. The aim of this design is to determine the service life of a component. This is to find the perfect measure of lightweight construction and strength.
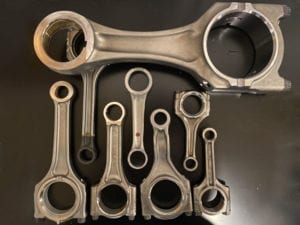
Design of components
Necessity of operational strength certificates
Fatigue strength considers the failure behavior of components under cyclic loading.
Components, materials and mechanic systems are usually subjected to both static and dynamic loads. The static load refers to the system at rest. The dynamic load refers to the moving system, e.g. oscillating or impacting stress. In addition, this has a greater influence on the mechanic system, which means that failure usually occurs even at lower stresses.
Therefore, in addition to a static strength verification, a dynamic verification must always be performed.
This strength verification is divided into two types of stress amplitude:
- constant load amplitude:
Execution with Wöhler tests (single-stage vibration tests). - time-variable load amplitude:
Operating load tests or fatigue tests.
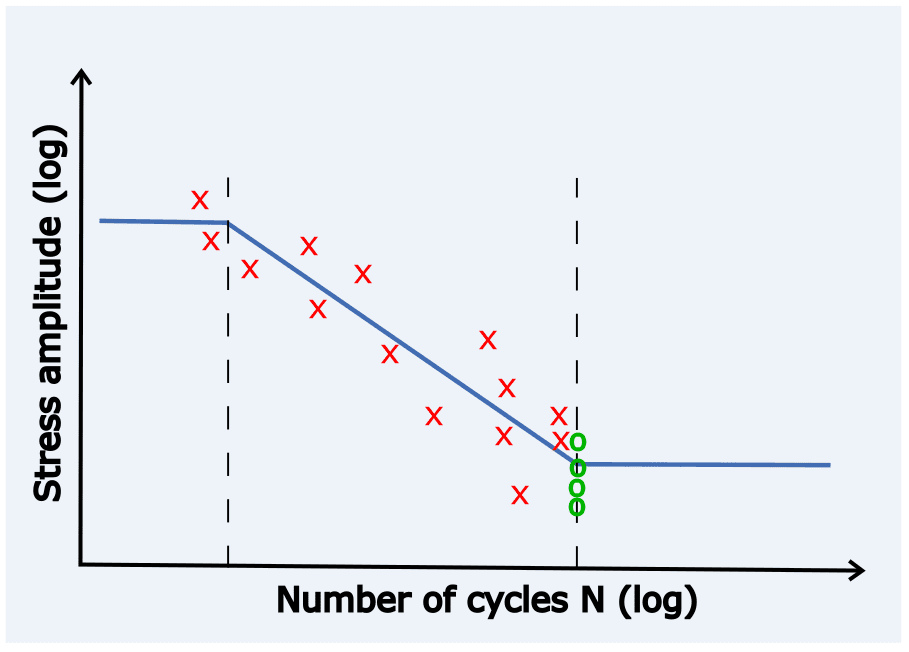
Experimental determination of the fatigue strength
Method for determining the operational strength
Wöhler tests
A fatigue test at constant load amplitude is also called a Wöhler test. During this test, a component or specimen is loaded cyclically, often with a sinusoidal load-time function. This means that the load changes within one oscillation period and is then repeated.
Operating load tests
In order to also take into account a load with a time-varying amplitude in the test, so-called real-time tests or operating load tests are carried out.
For this purpose, a realistic load signal of the component is first recorded. Here, the subsequent area of use and the associated subsoil (e.g. highway, dirt roads, etc.) must be taken into account.
The recorded signal can then be reproducibly displayed with a controller and reproduced on a test rig. This makes it possible to test the load influence on individual components during subsequent trials.
Tests with standardized load sequences
Over time, the results of the operating load tests have led to standardized, test-part-specific load sequences that are used internationally to measure dynamic stress.
Influences on the operational stability
- load type (tension, compression, bending, torsion)
- environmental test conditions (pressure, temperature, humidity, corrosion)
- design (notches, threads, radii)
- manufacturing process (welds)
- material condition (quenched and tempered, hardened)
In addition to these influencing parameters, the material of the component also plays an important role in fatigue strength. For example, structural steel and carbon fibre reinforced plastics (CFRP) have a significantly higher fatigue strength than plastic and glass fibre reinforced plastics (GFRP).
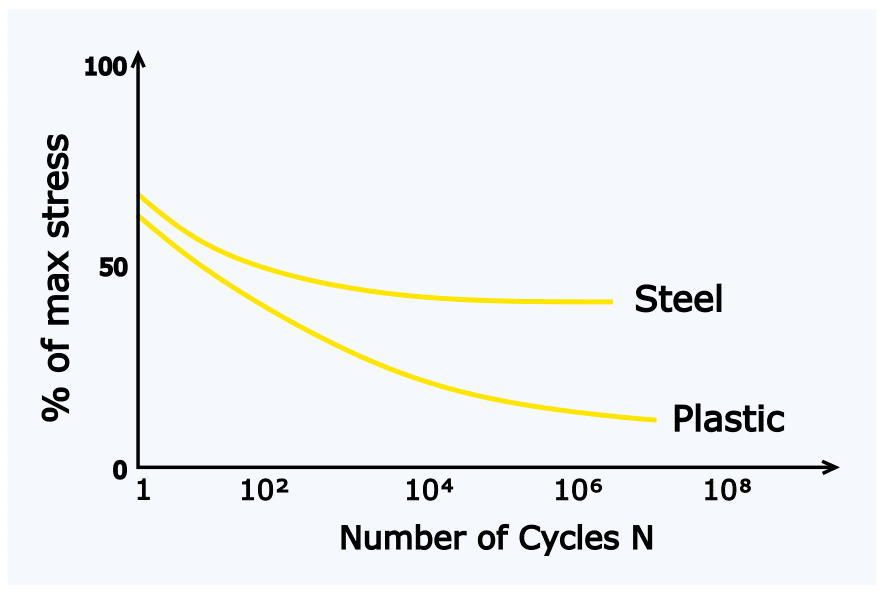
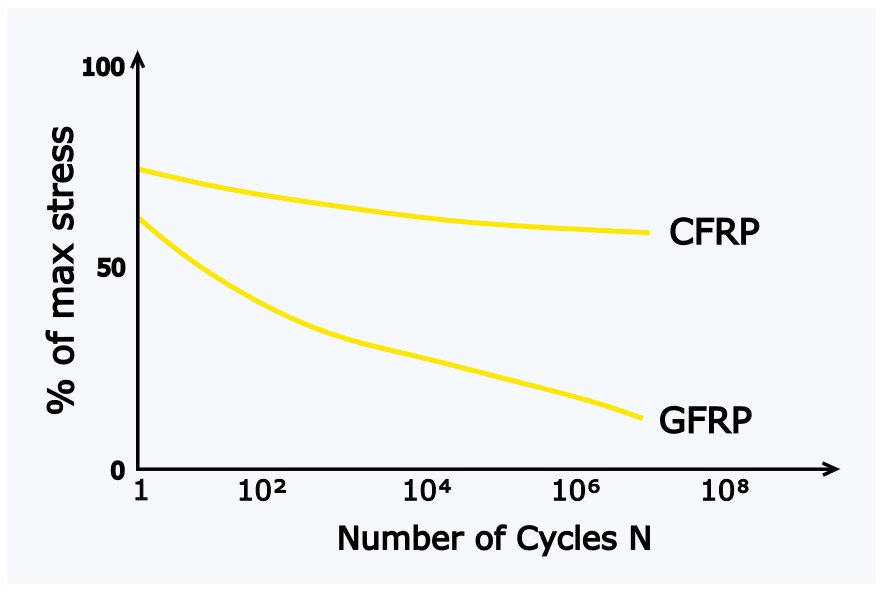
Explanation of terms
- Fatigue-resistant design:
The component must be able to withstand the oscillating stress continuously, i.e., any number of times, without breaking. - Operationally stable design:
The component must be able to safely withstand the oscillating stress without failure for the service life of the component, i.e. for a limited period of time.
Load cycles:
Oscillation cycle : A run of the different stress states of the test at constant load amplitude.
Number of oscillations : The total number of repeated oscillations.
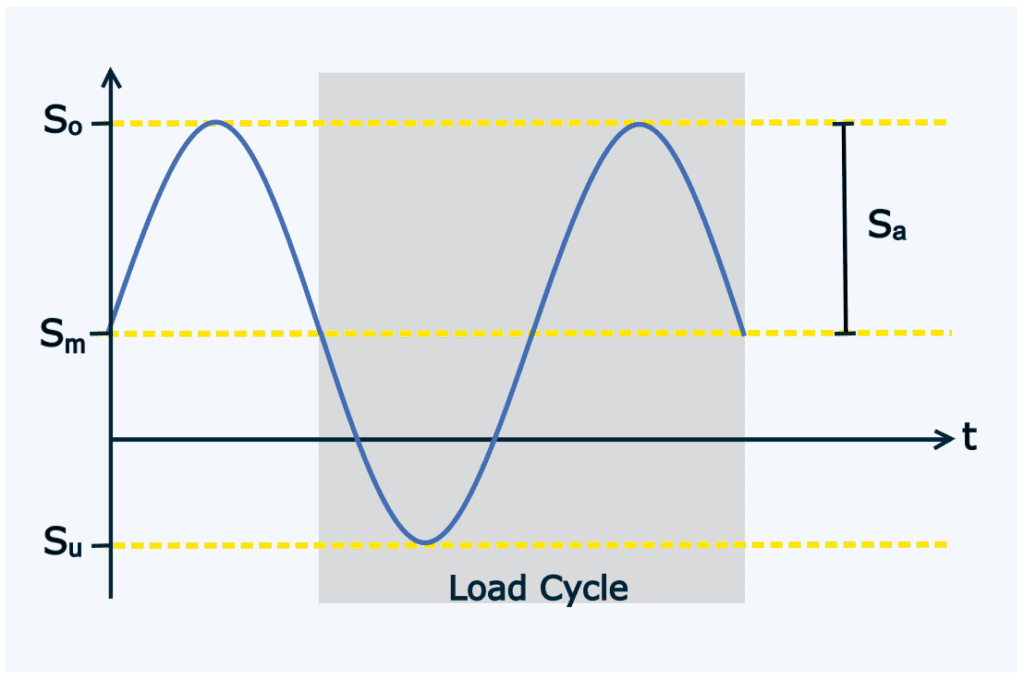
- S – nominal load
- Sₒ – upper load
- Sₘ – mean load
- Sₐ – load amplitude
- 2⋅Sₐ – oscillation amplitude
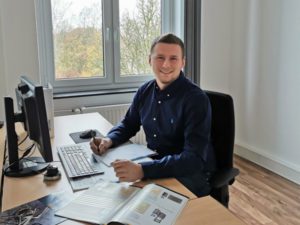
How can we help you?
When it comes to testing your products, components or assemblies for their load capacity, service life and reliability, we have the right solution. Please briefly describe your problem, we will be happy to get back to you in a timely manner!